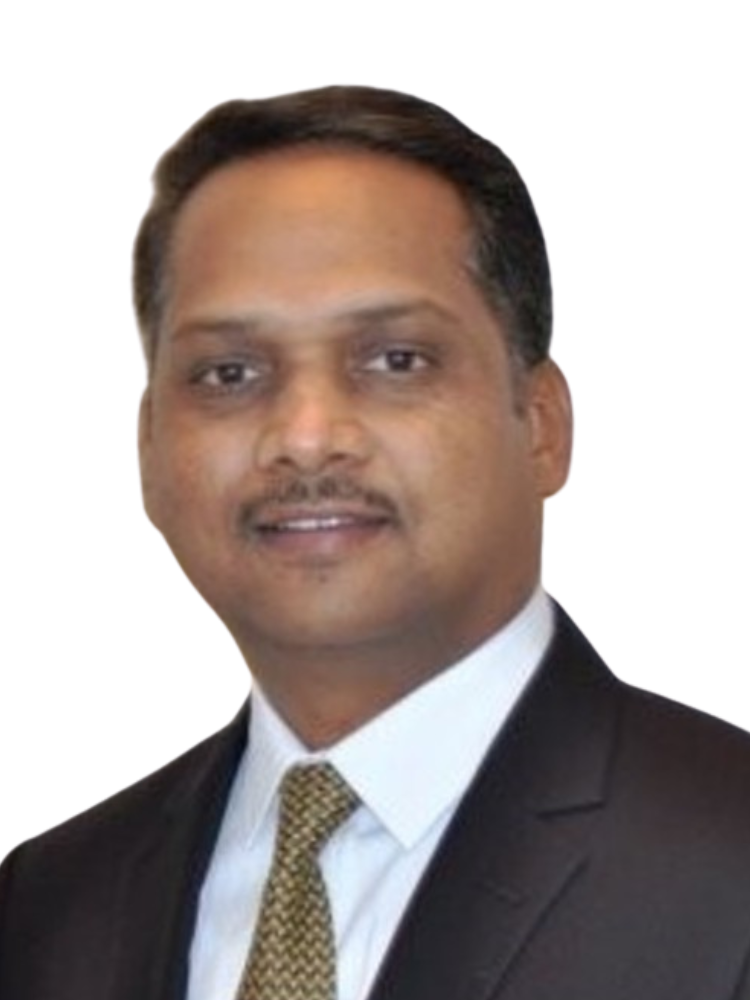
Mr. Balaji (Baala) Viswanathan
Lean Six Sigma Black Belt Consultant.
Senior Consultant
Lean Sigma Experts Australia (ABN 81 604 347 604)
- Lean and Process Improvement Specialist
- Varied industries, diverse people and multiple function experience within MEAP region
- Experienced in implementing process improvement initiatives from grass root levels
- Experienced professional in implementing Quality Management System aligning standard operating procedures towards continual process improvement
- Passionate trainer in Lean, Root Cause and Corrective Action and Competence Management
Professional Experience
Qualification
- EMBA in Operations from SP Jain School of Global Management, Dubai, UAE
- Eng in Mechanical Engineering from Bangalore University, India
- IASSC Certified Lean Six Sigma Black Belt
- Exemplar Certified ISO 9001:2015 (QMS) Lead Auditor
- Certified API Q2 Lead Auditor for Oil and Gas Industry
- Lean Trainer
Expertise
- Lean Six Sigma and Lean Deployment Training and Facilitation.
- Lean Six Sigma Project Consultancy and Training Material Development.
- Project Quality Plan and Business Process Improvement
- ISO 9001 and API Q1 / API Q2 (Oil and Gas) – Implementation and Auditing
- Project Management and Project Coordination activities in Process Improvement.
Major Achievements
- Led project towards achieving zero customer complaints in a year
- Led project towards 42% reduction in time to close outstanding corrective and preventive actions
- Led project towards 40% annual cost reduction in gauge management using DMAIC processes
- Championed cost of poor quality reduction projects using LSS methodologies resulting in 25% annual savings
- Led HR management implementation using process mapping, post-merger
- Integrating Quality Management Systems for a unified multisite certification for ready-mix operations
- Languages: English, Tamil and Hindi.
Credentials
Mr. Balaji graduated from Bangalore University, India with Bachelors in Mechanical Engineering. He also holds an Executive Master of Business Administration from SP Jain School of Global Management, Dubai, UAE, specializing in Operations Management. Mr. Balaji was assigned by his employer to leadership development programs in 2006 at Stanford University in the US, INSEAD in France and Tec De Monterrey in Mexico to gain an exposure in areas of leadership, strategic thinking, market strategy and general business. This is also backed with years of experience in different industries ranging from turnkey engineering, automotive component, construction material and oil & gas on manufacturing and service side of business. He is IASSC certified Black Belt and a certified lead auditor for ISO 9001:2015 and API Q2 (Oil and Gas). He has held several leadership facing roles climbing through the ranks in every organization and has worked in India, UAE, Singapore, Malaysia and in Australia, where he currently resides.
Experience
Mr. Balaji has 20 years of experience of which over 14 years have been in field of quality assurance and process improvement as a Quality Manager. He has implemented quality management systems to different global standards, led and participated in implementing process improvements in several manufacturing plants. He has trained several employees on interpretation of the ISO 9001 standards and Lean with the biggest gains being ownership of process improvements at operator level in the shop floor. He has experience in other functions including sourcing and supplier management, HSE, HR and factory management, appreciating how each function can add value to the overall productivity of an organization and towards implementing an effective business management system
- Working with all levels of the workforce implementing systems and driving change using PDCA process at an entry level of change
- Training middle management on Lean, Six Sigma Methodologies to equip with process driven changes
- Collaborating with middle management team to initiate, lead and take ownership of DMAIC projects as an outcome of operational issues, internal audit findings and customer complaints
- Performing Kaizen Blitz with teams that require rapid changes and improvements
- Mentoring and guiding towards implementation of actions towards realizing benefits of changes
- Setting up platforms for project owners at all levels to present on outcome of improvements to the leadership team
- Communicate periodically to the leadership team using SWOT as a basis of process improvement progress
- Creating SOPs, process flows and manuals towards implementing quality management systems
- Consulting and assisting towards accreditation to international quality standards
- Implementing HR planning and development tools including employee grading and band formalization/equalization, job posting and talent acquisition, employee surveys and improvement, salary surveys, career planning and employee development and succession management
Our Consultants
Request an Appointment
Get in touch with us for a free consultation on how we can assist with you or your organizations Lean Six Sigma training and certification needs.